介绍电感磁芯振动盘
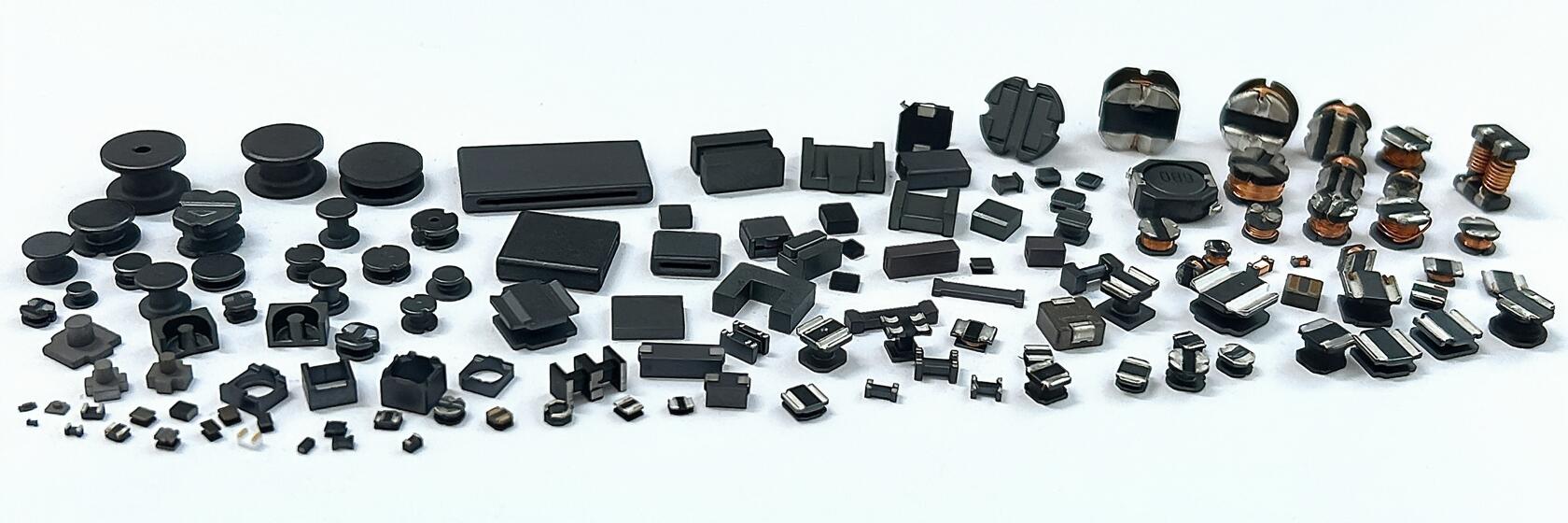
关于电感和磁芯
电感是最常用的电子元件之一,电感的种类繁多,很多电感是由磁芯绕线而成的,磁芯是这些电感的最核心组件。不同的电感对应有不同形状规格的磁芯,主要分类有:E型磁芯、U型磁芯、工字电感、环形磁芯、PQ型磁芯、EP型磁芯、 EFD型磁芯 等等。每个类别之下还有细分的不同尺寸规格。
电感的生产工序
电感在生产的过程中要经过上银、绕线、焊锡、点胶、测包等工序,有的空磁芯还需要经过外观检测。这些制程的每一个工序都对应一种或多种自动化设备。无论是对于还没绕线的空磁芯,或是已绕线的半成品还是等待最后检测的电感成品,设备要解决的首要问题就是如何实现自动化上料。铝合金振动盘在电感制造行业有非常广泛的应用。
电感生产的自动送料问题
对于电感元件的送料,铝合金振动盘在稳定性、可重复性、送料速度、降低破损的方面都明显优于不锈钢振动盘。早期由于铝合金振动盘的生产成本高,普及率低,电感设备曾经有很多是配置不锈钢振动盘的。但随着设计软件的进步和精密五轴数控机床的普及,铝合金振动盘在电感制程的用量占比越来越高。
电感形状规格种类有很多,生产过程得工序又很多,每个工序对应得振动盘的物料出料姿态和速度要求也不同,有时同一工序不同自动化设备生产厂家的做法不同对振动盘要求也不同。
比如绕线机要求速度不高,每分钟产量多数是几十个,但是一般生产厂家都要求一个人要同时看了很多台机器,所以对稳定性的要求很高。测包机的产量是200-400个/分钟之间。外观检测机对速度要求是最高的,随着相机技术的发展,相机每分钟能检测它的数量越来越大,振动盘的速度成为了检测机的瓶颈。检测机对振动盘的速度要求都是越快越好,对于多数小尺寸的磁芯,速度要求达1000个/分钟,甚至更高。
不同设备直振轨道出口的对接方式也不同。有的直轨出口是堵住的,设备直接在直振轨道末端用真空吸盘把磁芯吸走;有的直轨出口是打开的,磁芯进入设备的模块再被取走;而外观检测机振动盘的直线轨道一般都是往下倾斜5°的,这样有利于轨道跟玻璃盘的对接尽量靠近,(如下图)避免零件落在玻璃盘上而改变姿态。
CD和NR电感磁芯振动盘标准化
由于上面的原因电感磁芯振动盘的做法和规格就有很多,很难形成一个统一的标准。
CD电感和NR电感的制程中振动盘应用的最多。我们经过多年专注于电感磁芯振动盘的研发,形成了CD磁芯和NR磁芯大部分型号的振动盘的标准化。客户订购前只要告知我们以下信息,我们就有对应的产品。这样大大降低了生产周期,节约了成本,采用我们成熟的产品还降低了客户的采购风险。
1.磁芯或电感的型号和尺寸规格。
2.用在什么设备上。
3.顺时针还是逆时针。
4.出料姿态。
对于CD磁芯一般都是出口管住平位出料的。如图,只有锡面向上和锡面向下两种可能的姿态。
对于NR磁芯分别如图,四种出料方式分别称为:锡向上==出料,锡向上11出料,锡向下==出料,锡向下11出料。
5.出料速度要求。
6.盘面大小要求。
CD磁芯振动盘传统的做法是盘面跟直线轨道直接对接,由于磁芯的尺寸有一定的误差,盘面出口必须有0.2mm或更大的间隙。这时零件就会由于在对接口旋转一定角度导致卡料发生。
我们采用开放式的对接方法很好的解决了这个问题,如图。
磁芯在盘面出口处是开放并倾斜的,磁芯送进直轨的模块后,通过气吹把平位没有靠住底线的物料吹回盘内,这样就避免了卡料的发生。正确的物料会在模块上扭平再送进直线轨道。
优先采用机械结构的选料方式
我们设计的磁芯振动盘都遵循尽量不使用或少用传感器的原则。光纤、光电、接近开关等传感器的应用常常会实现机械结构很难做得到的选料要求。但是过多的使用传感器会有以下的缺点:
1. 增加设备的调试和使用难度。
2. 由于物料的新旧程度不同或光泽不同导致误判。
3. 气压或传感器延时设定等因素会影响稳定性和准确率。
4. 增加了设备成本。
图示光纤聚焦光点打在零件表面上,零件不同位置反射率不同,可以根据光纤放大器接收到的反射光量大小来判断零件是OK的还是NG的,NG的零件会被吹回盘内。当反光量差异不大时,这种做法有误判的可能。
共模电感磁芯的送料,一般的做法是用光纤传感器来分辨零件的姿态,但是我们是通过挂住底部的小槽来实现选别的。对于小槽向上的出料方式,挂住槽后,通过翻转模块把零件再翻转过来。小槽的尺寸只有0.15*0.15mm, 这样的选别方式对选料零件的凸线的加工精度、对振动盘的底座频率和稳定性都有很高的要求。我们生产的精密高频底座能用这种方式实现共模电感的精确平稳送出。